Disinfectant Fogging for Cleanrooms
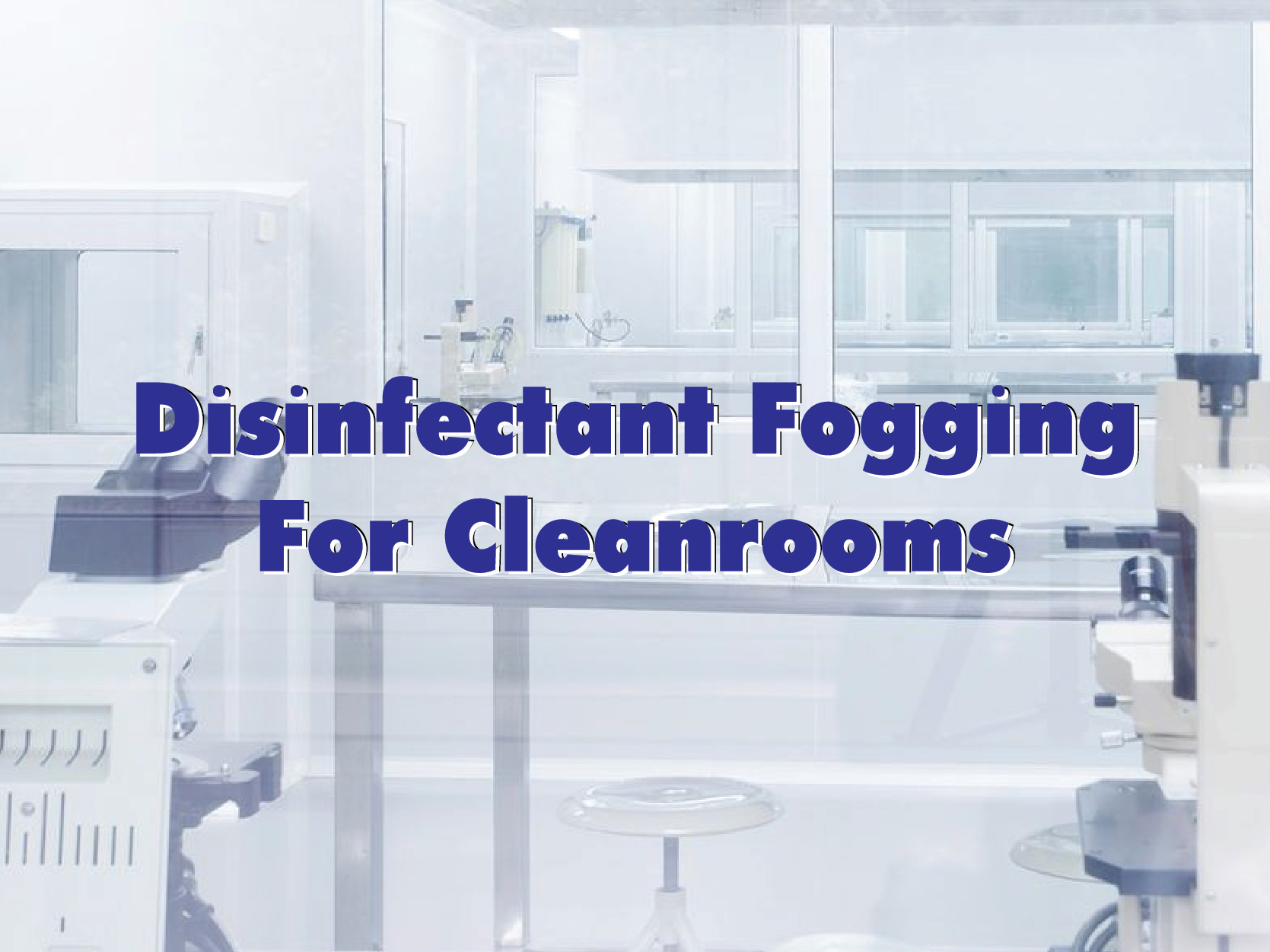
End of production cleaning and disinfection is selective to food contact surfaces and can lead to the potential survival of micro-organisms in the wider environment. Whole room disinfection enables difficult-to-reach places to be thoroughly disinfected, as Dr Karen Middleton, of Campden BRI, explains.
Disinfectant fogging is a technique that has become increasingly popular in the cleanroom industry as a way to maintain a sterile environment. In this article, we will discuss what disinfectant fogging is, how it works, and why it is an effective solution for cleanrooms.
What is Disinfectant Fogging?
Disinfectant fogging is a process of releasing a fine mist of disinfectant solution into the air of a cleanroom to sanitize all surfaces and reduce the risk of contamination. The disinfectant solution is atomized using a specialized machine, creating a fog that spreads evenly throughout the room.
How does Disinfectant Fogging Work?
The disinfectant solution used in fogging contains chemicals that are effective at killing bacteria, viruses, and other microorganisms. The fogging machine creates a mist that disperses the disinfectant solution in the air, covering all surfaces and hard-to-reach areas.
The fogging process creates a fine mist that is small enough to reach even the tiniest crevices and corners of a cleanroom. As the mist settles on surfaces, it disinfects them by killing any microorganisms present.
Why is Disinfectant Fogging an Effective Solution for Cleanrooms?
Cleanrooms are designed to be sterile environments, but they can be easily contaminated by microorganisms. Disinfectant fogging is an effective solution for cleanrooms because it can reach all areas of the room, including surfaces that are difficult to access using traditional cleaning methods.
Disinfectant fogging is also a time-efficient solution. The process can be completed quickly, and the room can be used again shortly after fogging has been completed. This means that cleanrooms can remain in operation, reducing downtime and increasing productivity.
Additionally, disinfectant fogging is an environmentally friendly solution. The fogging solution used is non-toxic, and there is no residue left behind after the fogging process is complete. This means that the cleanroom can remain sterile without the need for harsh chemicals or extensive cleaning procedures.
Both the pharmaceutical and clinical sectors have been targeted by a range of whole room type decontamination systems, but their practical operation and benefit in the food and drink industry is relatively unknown. The range of techniques is increasing, but those that are commercially available include:
• Chemical Fogging
• Vaporised Hydrogen Peroxide
• Ozone
• Chlorine Dioxide
• Ultraviolet Light
• Titanium Dioxide Coating and UV Light
• Ionisation
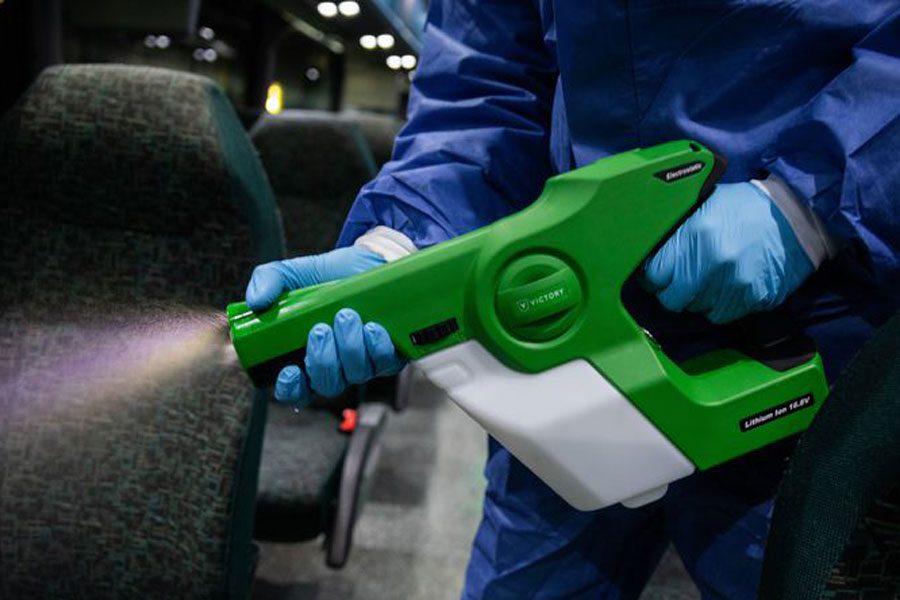
Chemical Fogging
Chemical fogging is a process used for disinfecting and sanitizing indoor spaces by applying a fine mist of chemical disinfectant throughout the room. This method is commonly used in hospitals, laboratories, food processing plants, and other facilities where a high level of cleanliness is required.
During chemical fogging, the disinfectant is converted into a mist or fog using a machine, which then fills the entire area, including hard-to-reach places. The mist settles on surfaces, objects, and even the air, killing any pathogens or viruses present in the environment.
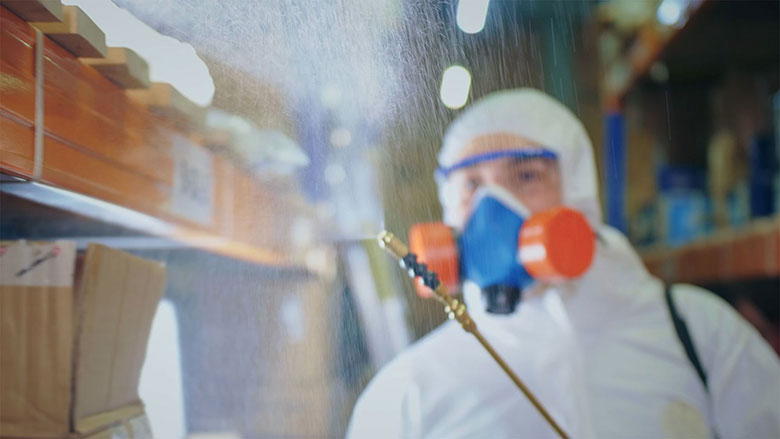
Vaporized hydrogen peroxide
Vaporized hydrogen peroxide (VHP) is a method of disinfection commonly used in healthcare settings and other industries to decontaminate surfaces and equipment. VHP is a sterilization method that uses hydrogen peroxide in its vaporized form to kill microorganisms, including bacteria, viruses, and fungi.
The process of VHP involves vaporizing a solution of hydrogen peroxide and then dispersing the vapor throughout the space to be decontaminated. The hydrogen peroxide vapor reacts with the microbial cells, disrupting their structure and function, and ultimately killing them.
Ozone
High reactivity, penetrability and spontaneous decomposition into a non-toxic product make ozone a viable disinfectant for use in food production areas. Due to its reactive, unstable nature, ozone is produced at the point of use. Ozone generators effectively pass air through a high-energy source, such as UV light or corona discharge within the equipment, which leads to the formation of ozone. A typical decontamination cycle consists of three phases in a one-step process: humidification to 70–80%; decontamination, where the ozone vapour concentration increases rapidly to 8–25ppm and is maintained at an optimum biocidal level by the ozone generator; and aeration. One manufacturer utilises a biocidal quenching agent that further mops up the remaining ozone leaving the room clean, safe and fresh for immediate re-occupation. Cycle times vary depending on the area volume, desired level of decontamination and area contents, but are typically between 30 and 90min.
Chlorine dioxide
ClO2 gas is considered environmentally friendly as it rapidly breaks down into innocuous sodium salts. It is unstable and therefore is generated at its site of use by various chemical and electro-chemical methods. It has been shown to be effective at 2mg L-1 and at >65% relative humidity for 12hrs. Mobile and fixed ClO2 generator systems that allow automation of the application are commercially available.
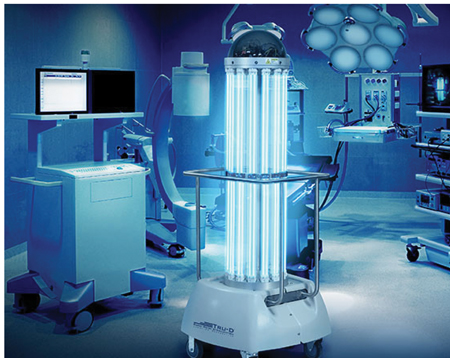
Ultraviolet light
Ultraviolet (UV) light is often used in cleanrooms to sterilize surfaces and equipment to prevent the growth and spread of microorganisms. UV light with a wavelength of 254 nanometers (nm) is particularly effective in destroying the DNA of bacteria, viruses, and other pathogens.
UV light can be applied in several ways in cleanroom settings. One common method is to install UV lamps in the ceiling or walls of the cleanroom. The lamps emit UV-C light, which can kill microorganisms on surfaces and in the air. However, UV-C light can also be harmful to human skin and eyes, so precautions must be taken to ensure that personnel are not exposed to the light.
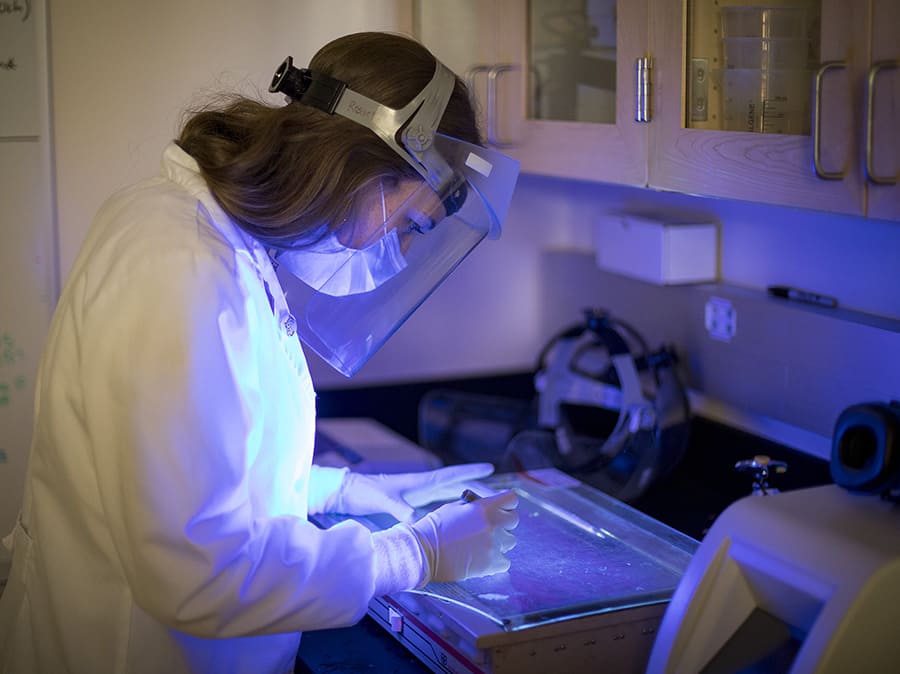
Titanium dioxide
Titanium dioxide (TiO2) is a photocatalytic material that can be used to create a self-cleaning coating for cleanrooms. When exposed to ultraviolet (UV) light, TiO2 produces reactive oxygen species that can break down organic compounds and bacteria on the surface of the coating.
The self-cleaning properties of TiO2 coatings can reduce the need for manual cleaning and disinfection in cleanrooms, which can help to minimize the risk of contamination. Additionally, the use of TiO2 coatings can reduce the use of cleaning chemicals, which can be harmful to the environment and may cause skin irritation or respiratory problems in workers.
UV light is necessary for the photocatalytic properties of TiO2 to be activated. Therefore, it is important to ensure that there is sufficient UV light exposure in the cleanroom to activate the TiO2 coating. This can be achieved through the use of UV lamps or natural sunlight, depending on the design of the cleanroom.
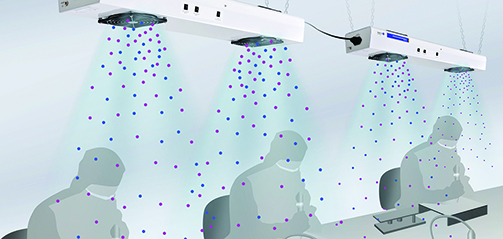
Ionisation
Ionisation is a commonly used technique in cleanrooms to neutralize static charges and reduce particle contamination. The process involves the introduction of ions into the cleanroom environment, which interact with charged particles and neutralize them.
There are two main types of ionisation methods used in cleanrooms:
1. Corona ionisation: In this method, a high voltage is applied to a sharp pointed electrode, which creates a corona discharge that generates ions. These ions then neutralize any charged particles in the air.
2. Nuclear ionisation: This method involves the use of a radioactive source, which emits alpha, beta, or gamma particles. When these particles interact with air molecules, they produce ions that neutralize any charged particles in the environment.
Both methods have their advantages and disadvantages. Corona ionisation is a non-radioactive and low-cost method, but it requires periodic maintenance and can produce ozone. Nuclear ionisation, on the other hand, is a more expensive and complex method but provides continuous ionisation without any maintenance requirements.